Ferramentaria para Moldes de Injeção: Guia Completo
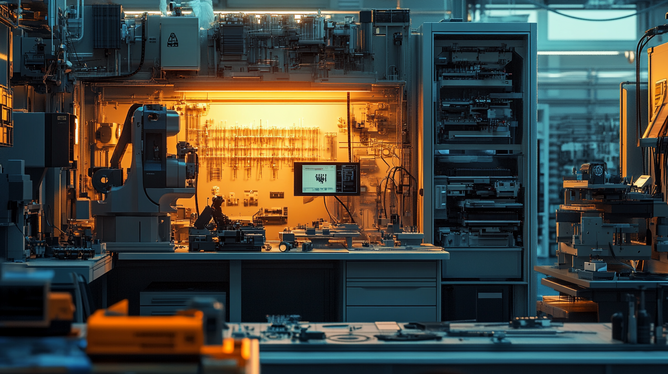
Por: Antonio - 11 de Outubro de 2024
A Ferramentaria moldes de injeção desempenha um papel crucial na indústria de manufatura, permitindo a produção em massa de peças com alta precisão. Neste artigo, vamos explorar os principais aspectos dessa técnica, desde os materiais utilizados até as vantagens de sua aplicação. Você irá aprender sobre os processos envolvidos e como a manutenção adequada pode prolongar a vida útil dos moldes. Continue lendo e descubra tudo o que precisa saber para otimizar sua produção.
O que é Ferramentaria de Moldes de Injeção
A Ferramentaria de Moldes de Injeção é um ramo especializado da engenharia e manufatura que se concentra na criação de moldes usados no processo de injeção de plásticos e outros materiais. Este método é amplamente utilizado na produção de peças e componentes para diversas indústrias, como automotiva, eletrônica e bens de consumo. Com a crescente demanda por produtos com formas complexas e alto grau de detalhamento, a ferramentaria tornou-se um elemento essencial para a fabricação em larga escala.
O processo de moldagem por injeção consiste em derreter um material, geralmente plástico, e injetá-lo sob pressão em um molde previamente fabricado. Quando o material esfria e solidifica, ele toma a forma do molde, resultando em uma peça final que pode ser utilizada em diversos produtos. A eficiência desse processo está diretamente relacionada à qualidade e precisão do molde, tornando a ferramentaria crucial para garantir a eficácia da produção.
A construção de moldes de injeção envolve várias etapas, começando pela concepção do design. Designers e engenheiros trabalham em conjunto para criar um modelo tridimensional da peça desejada. Esse modelo é essencial para a confecção do molde, que é feito de materiais resistentes, como aço ou alumínio, capazes de suportar a pressão e a temperatura do material injetado.
Após a fase de design, a próxima etapa é a usinagem do molde, onde máquinas CNC (Controle Numérico Computadorizado) são frequentemente utilizadas. Essas máquinas permitem um alto nível de precisão na fabricação dos moldes, o que é fundamental para garantir que cada peça produzida mantenha os padrões de qualidade exigidos. O controle preciso das dimensões e tolerâncias é vital, pois pequenos erros podem comprometer a funcionalidade da peça final.
A montagem do molde também é uma etapa importante do processo. Os moldes são compostos por diversas partes, incluindo cavidades, canaletas de resfriamento e componentes de ejetores. A integração desses elementos deve ser feita com precisão, pois cada um desempenha um papel fundamental na eficiência do processo de injeção. O resfriamento adequado do molde é crucial para garantir que o material solidifique na forma correta e em um tempo ideal, otimizando a produtividade.
Outro aspecto negativo da ferramentaria de moldes de injeção é o custo envolvido. A fabricação de um molde pode ser dispendiosa, e isso pode representar um desafio para pequenas empresas. Entretanto, com a crescente necessidade de produção em massa e a economia de escala que a moldagem por injeção proporciona, o investimento em ferramentaria torna-se frequentemente justificável a longo prazo.
Além disso, a manutenção dos moldes é um aspecto crucial que deve ser considerado. Moldes de injeção estão sujeitos a desgaste, o que pode afetar a qualidade das peças produzidas. Por isso, é essencial estabelecer um plano de manutenção preventiva que inclua limpeza, lubrificação e inspeções periódicas. A manutenção proativa pode evitar falhas durante a produção e aumentar a vida útil do molde.
Em resumo, a Ferramentaria de Moldes de Injeção é uma técnica fundamental para a fabricação de peças de alta qualidade e precisão. O processo envolve várias etapas, desde o design inicial até a usinagem e montagem, exigindo um alto nível de especialização e tecnologia. Com o avanço das técnicas de fabricação e a crescente demanda por produtos inovadores, a importância da ferramentaria na indústria não pode ser subestimada. Ao investir em moldes de injeção bem projetados e mantê-los corretamente, as empresas podem maximizar a eficiência de seus processos produtivos e garantir a excelência de seus produtos.
Principais Materiais Utilizados na Fabricação
A fabricação de moldes de injeção é uma disciplina que demanda não apenas experiência técnica, mas também a escolha adecuada de materiais. Os materiais utilizados na construção dos moldes precisam ser selecionados cuidadosamente, pois possuem um impacto direto na durabilidade, na precisão e no custo da produção. Neste artigo, vamos explorar os principais materiais utilizados na fabricação de moldes de injeção, destacando suas características e aplicações.
Um dos materiais mais comuns na fabricação de moldes de injeção é o aço. O aço é escolhido por sua resistência e versatilidade. Existem vários tipos de aço que podem ser utilizados, como o aço endurecido, que é ideal para moldes que passarão por um desgaste intenso. O aço inoxidável também é uma opção popular, especialmente em aplicações onde a corrosão é uma preocupação. A principal vantagem do aço é sua capacidade de suportar altas temperaturas e pressões sem deformação, o que é essencial em processos de injeção.
Outro material amplamente utilizado é o alumínio. Embora o alumínio seja menos resistente que o aço, ele possui a vantagem de ser muito mais leve. Isso pode facilitar o manuseio e a instalação dos moldes. Além disso, o alumínio tem uma capacidade de dissipação de calor superior, o que é benéfico para processos de resfriamento rápido. Por conta desses atributos, o alumínio é frequentemente utilizado em moldes de produção em baixa quantidade ou em aplicações onde o custo é uma preocupação maior.
Os polímeros especiais também estão ganhando destaque na fabricação de moldes de injeção. Materiais como o nylon e o policarbonato podem ser usados em aplicações específicas que requerem maior flexibilidade ou resistência ao impacto. Esses materiais são ideais para a produção de peças complexas que exigem um nível elevado de detalhamento. Apesar de sua natureza térmica, eles podem ser eficazes em moldes para injeção de plásticos que não geram altas temperaturas durante o processo.
Outro aspecto importante a considerar é a superfície dos materiais utilizados. As propriedades da superfície podem influenciar a facilidade de extração da peça moldada. Materiais com acabamentos polidos ajudam a reduzir o atrito, facilitando a retirada da peça do molde. Por isso, é comum o uso de revestimentos que aumentam a resistência à abrasão e à corrosão, como o nitretos e revestimentos de PVD (Deposição de Vapor em Fase Física), que podem ser aplicados tanto em moldes de aço quanto de alumínio.
Além disso, a tratamento térmico é uma prática comum que procura maximizar as propriedades mecânicas dos materiais utilizados. O tratamento térmico pode aumentar a dureza do molde, tornando-o mais resistente ao desgaste, isso é particularmente relevante para moldes que serão utilizados em altas quantidades de injeções. Existem diferentes tipos de tratamentos térmicos que variam em intensidade e objetivos, como a têmpera, que pode garantir uma estrutura interna mais rígida e durável.
A escolha do material também deve levar em conta o custo. Materiais mais nobres geralmente apresentam um custo mais elevado, mas oferecem benefícios que podem justificar esse investimento, principalmente em produções de grande escala. Por outro lado, o uso de materiais de baixo custo pode ser adequado para aplicativos que não exigem uma durabilidade extrema.
Por último, não devemos esquecer da importância da sustentabilidade na escolha dos materiais. Com a crescente preocupação ambiental, muitos fabricantes estão optando por materiais recicláveis ou que têm um impacto ambiental menor. A utilização de plásticos de origem biológica e a reciclagem de materiais estão se tornando cada vez mais comuns na indústria.
Em resumo, a seleção do material na fabricação de moldes de injeção é uma parte crítica do processo. A decisão deve considerar fatores como durabilidade, custo, propriedades térmicas e impactos ambientais. Com a combinação adequada de materiais e técnicas, é possível produzir moldes que atendam aos mais altos padrões de qualidade e eficiência, assegurando um processo de injeção bem-sucedido.
Processos Envolvidos na Criação de Moldes
A criação de moldes de injeção é um processo complexo que envolve uma série de etapas interligadas, cada uma delas essencial para garantir a qualidade e a precisão das peças produzidas. Neste artigo, vamos explorar os principais processos envolvidos na fabricação de moldes, desde a concepção até a finalização, proporcionando uma visão abrangente do que está por trás desse importante aspecto da engenharia e manufatura.
O primeiro passo no processo de criação de moldes é a definição do projeto. Essa etapa envolve a colaboração entre engenheiros de design e especialistas em engenharia de moldes para desenvolver um modelo que atenda às especificações desejadas. Utilizando softwares de modelagem tridimensional, como CAD (Desenho Assistido por Computador), os profissionais criam peças virtuais que permitem visualizar a geometria final. Durante essa fase, são consideradas as requisitos técnicos, como dimensões, tolerâncias e características funcionais, assegurando que o molde final se encaixará perfeitamente nas necessidades do produto.
Após a finalização do projeto, o próximo passo é a fabricação do molde. Essa fase inclui diversas tecnologias de produção, sendo a usinagem uma das mais comuns. Máquinas CNC (Controle Numérico Computadorizado) são empregadas para esculpir os materiais escolhidos, como aço ou alumínio, em conformidade com o modelo desenvolvido. O uso de máquinas CNC permite alta precisão e repetições consistentes, minimizando erros que podem comprometer a qualidade do molde.
Outra técnica envolvida na fabricação do molde é a fabricação aditiva, ou impressão 3D, que tem se tornado uma opção viável para a produção de protótipos e até mesmo moldes finais em alguns casos. A impressão 3D permite que os projetistas realizem testes de design mais rapidamente e com menor custo, possibilitando ajustes antes que o molde definitivo seja produzido.
Uma vez que o molde é esculpido, é necessário proceder com a montagem dos componentes. Um molde típico de injeção é composto por várias partes, como a cavidade, o núcleo e os canais de resfriamento, além de ejetores utilizados para a remoção da peça moldada. Essa montagem deve ser feita com atenção cuidadosa; qualquer imprecisão pode afetar o desempenho do molde e a qualidade da peça final.
A seguir, vem a etapa do tratamento térmico. Processos como têmpera e revenimento são frequentemente utilizados para aumentar a resistência e durabilidade do molde. O tratamento térmico modifica a estrutura cristalina do material, resultando em propriedades mecânicas superiores, o que é vital em aplicações que demandam alta performance. A escolha do tratamento adequado depende do tipo de material utilizado e das exigências do processo de injeção.
Após o tratamento térmico, a próxima fase é a finação e acabamento superficial. Esse processo inclui polimento e revestimento do molde, visando garantir uma superfície lisa que facilite a extração da peça moldada e reduza o atrito durante o processo de injeção. Acabamentos de qualidade são cruciais para evitar defeitos na peça final, como marcas ou falhas de superfície.
Depois que todas as etapas de fabricação e acabamento estão concluídas, é hora de realizar testes e validações. Esses testes são fundamentais para garantir que o molde atenda às especificações de design e funcionalidade. Normalmente, um molde passa por uma série de injeções de teste, onde o desempenho é avaliado e ajustes são feitos, se necessário. Este passo é crucial para identificar problemas antes que o molde entre em produção em larga escala.
Finalmente, uma vez que tudo esteja validado, o molde é preparado para a produção em massa. Essa fase envolve a definição das configurações da máquina de injeção, seleção dos materiais a serem utilizados e ajustes dos parâmetros de injeção, como temperatura e pressão. O controle rigoroso desses fatores é essencial para garantir a qualidade e a consistência das peças fabricadas.
Em suma, a criação de moldes de injeção é um processo intricado que exige precisão e atenção em cada etapa, desde o design inicial até a preparação para a produção em massa. Compreender esses processos é vital para qualquer profissional que deseja se aventurar na indústria de fabricação, garantindo que as peças moldadas atendam aos mais altos padrões de qualidade e desempenho.
Vantagens da Utilização de Moldes de Injeção
A moldagem por injeção é uma técnica amplamente utilizada na fabricação de peças plásticas e de outros materiais, devido às suas inúmeras vantagens. O uso de moldes de injeção oferece benefícios significativos em comparação com outras metodologias de produção, tornando-o uma escolha preferencial para muitas indústrias. Neste artigo, discutiremos as principais vantagens da utilização de moldes de injeção.
Um dos maiores benefícios da moldagem por injeção é a eficiência na produção em massa. Este método permite a fabricação rápida de grandes quantidades de peças idênticas a partir de um único molde. Uma vez que o molde está criado e testado, ele pode ser utilizado repetidamente para produzir dezenas, centenas ou até milhares de peças sem necessidade de ajustes significativos. Essa característica é especialmente valiosa em indústrias onde a demanda por produtos é alta e a velocidade de produção é crucial.
Além da eficiência, a precisão e a consistência são características notáveis da moldagem por injeção. Os moldes são fabricados com tolerâncias extremas, o que significa que as peças produzidas são altamente precisas e homogêneas. Isso minimiza a variação entre as peças e garante que cada unidade atenda aos padrões de qualidade, o que é fundamental em setores como o automotivo e o eletrônico, onde a precisão é tudo.
A flexibilidade de design também é um fator importante a considerar. A moldagem por injeção permite a criação de formas complexas e detalhadas que seriam desafiadoras ou até impossíveis de produzir por outros métodos. Isso abre um leque de possibilidades para designers e engenheiros, permitindo que eles explorem inovações criativas em seus produtos. Mesmo peças com características intrincadas, como designs com encaixes ou recortes precisos, podem ser fabricadas eficientemente.
Além disso, a redução de desperdício de material é uma das vantagens significativas da moldagem por injeção. O processo de injeção utiliza o material de forma eficiente, minimizando a quantidade de sobra ou desperdício. Isso é especialmente importante em um mundo que clama por práticas de fabricação mais sustentáveis e ambientalmente responsáveis. O uso efetivo dos materiais reduz os custos e o impacto ambiental, o que, por sua vez, pode melhorar a imagem da empresa entre consumidores e reguladores.
A moldagem por injeção também facilita a integração de múltiplos componentes em uma única peça. Isso significa que elementos como suportes, ranhuras ou até mesmo características funcionais podem ser incorporados no design original sem a necessidade de montagem adicional. Essa integração não só reduz os custos de produção, mas também diminui o tempo de montagem e melhora a durabilidade do produto final.
Outro ponto a favor da utilização de moldes de injeção é a variedade de materiais disponíveis para a moldagem. A tecnologia de injeção é compatível com uma ampla gama de plásticos e materiais compósitos, possibilitando que empresários e fabricantes escolham o mais adequado para suas necessidades específicas. Isso inclui plásticos de alta resistência, elastômeros que proporcionam flexibilidade e até mesmo materiais recicláveis, que são cada vez mais populares no mercado. Essa variedade permite que as empresas atendam a diferentes segmentos de mercado de forma ágil e eficiente.
Além disso, a facilidade de automação que a moldagem por injeção oferece é uma vantagem considerável. Muitas fábricas estão investindo em robótica e sistemas automatizados que podem operar máquinas de injeção 24 horas por dia. Isso não só aumenta ainda mais a eficiência do processo, mas também reduz a necessidade de intervenção manual, o que pode levar a menos erros e maior segurança no ambiente de trabalho.
Por último, mas não menos importante, o uso de moldes de injeção também traz um retorno sobre o investimento (ROI) favorável. Embora o custo inicial para construir um molde possa ser alto, a economia gerada pela produção em massa e a durabilidade dos moldes significa que, a longo prazo, o custo por peça geralmente é reduzido. Essa economia, quando somada a preços competitivos, pode resultar em margens de lucro substanciais para empresas que adotam essa tecnologia.
Em resumo, as vantagens da utilização de moldes de injeção são numerosas e impactantes. Desde a eficiência na produção em massa e a precisão na fabricação até a flexibilidade de design e a sustentabilidade, este método se destaca como uma escolha ideal para muitas aplicações industriais. Ao considerar todas essas vantagens, é fácil ver por que a moldagem por injeção continua a ser uma técnica de fabricação popular e eficaz.
Manutenção e Cuidados com Moldes de Injeção
A manutenção e os cuidados adequados com moldes de injeção são essenciais para garantir sua durabilidade e eficiência ao longo do tempo. Moldes mal mantidos podem levar a defeitos nas peças moldadas, reduzir a produtividade e até causar falhas nas máquinas, resultando em custos adicionais para a empresa. Este artigo aborda as melhores práticas de manutenção e cuidados que devem ser adotados para prolongar a vida útil dos moldes de injeção.
Um dos aspectos mais importantes da manutenção de moldes de injeção é a limpeza regular. Após o uso, é fundamental que os moldes sejam limpos cuidadosamente para remover resíduos de material, sujeira, lubrificantes e outros contaminantes. Qualquer resíduo acumulado pode afetar a precisão do molde e a qualidade da peça final. A limpeza deve ser feita com solventes apropriados e escovas que não danifiquem a superfície do molde. É importante também utilizar métodos de limpeza recomendados pelo fabricante dos materiais utilizados, evitando produtos que possam causar corrosão.
A inspeção periódica dos moldes é outra prática crucial na manutenção. Realizar inspeções regulares permite que os operadores identifiquem problemas antes que se tornem sérios. Durante a inspeção, deve-se verificar componentes críticos, como ejetores, canais de resfriamento e superfícies de contato. Qualquer sinal de desgaste, desgaste ou dano deve ser tratado prontamente para evitar impactos negativos na produção. A documentação das condições dos moldes durante as inspeções também pode ajudar a identificar padrões de desgaste e a planejar manutenções futuras.
A lubrificação adequada é fundamental para o funcionamento eficiente dos moldes de injeção. Os ejetores e outras partes móveis devem ser lubrificados regularmente para minimizar o atrito e garantir um funcionamento suave. A falta de lubrificação pode gerar desgaste excessivo, levando a falhas no sistema de ejetores, que podem resultar na peça moldada ficando presa no molde. A escolha do lubrificante é importante: deve ser compatível com os materiais envolvidos no processo e não deve deixar resíduos que possam afetar a qualidade da peça final.
Além disso, o reforço de superfícies do molde, como a aplicação de revestimentos protetores, pode ser uma estratégia eficaz para prolongar a vida útil do molde. Revestimentos como nitretos e outros tratamentos superficiais ajudam a proteger o molde contra desgaste e corrosão. Essas superfícies tratadas também são menos propensas a acumular resíduos, facilitando a limpeza. Tratamentos de superfície devem ser realizados por profissionais capacitados, garantindo que a aplicação seja feita corretamente.
A manutenção preventiva é uma estratégia recomendada para evitar problemas inesperados durante a produção. Isso envolve agendar paradas regulares para a realização de manutenção antes que ocorra uma falha. A manutenção preventiva pode incluir lubrificação regular, inspeções detalhadas, ajustes e substituições de peças conforme necessário. Criar um cronograma de manutenção baseado nas horas de operação ou na frequência de uso do molde pode ajudar a manter os moldes em boa condição.
Outro aspecto importante é o armazenamento adequado dos moldes quando não estão em uso. Os moldes devem ser armazenados em um local seco e limpo, longe de umidade e contaminantes. É aconselhável utilizar capas ou envoltórios protetores para evitar a exposição a poeira e sujeira. Além disso, todos os componentes móveis devem ser liberados antes do armazenamento para evitar deformações e garantir que os moldes mantenham sua capacidade de operação quando forem utilizados novamente.
A documentação também desempenha um papel importante na manutenção de moldes de injeção. Manter registros detalhados sobre a manutenção realizada, o histórico de inspeções e quaisquer reparos feitos nos moldes ajuda a identificar padrões de desgaste e a estabelecer melhores práticas. Esses registros podem ser utilizados para treinar novos operadores e para ajudar na tomada de decisões sobre quando um molde deve ser reparado ou substituído.
Por último, o treinamento da equipe que opera e mantêm os moldes é essencial. Profissionais bem treinados estarão mais atentos aos sinais de desgaste e entenderão a importância de seguir as práticas recomendadas de manutenção. Investir em treinamento e desenvolvimento da equipe é um passo importante para garantir a continuidade da produção e a qualidade das peças moldadas.
Em conclusão, a manutenção e os cuidados com moldes de injeção desempenham um papel crítico na eficácia e na longevidade desses componentes essenciais. A adoção de práticas recomendadas, como a limpeza regular, inspeções periódicas e lubrificação adequada, junto com um bom planejamento de manutenção preventiva, pode resultar em moldes mais duráveis e em um desempenho superior na produção. Ao aplicar essas diretrizes, as empresas podem maximizar a eficiência de seus processos de injeção e garantir a qualidade das peças fabricadas.
Tendências e Inovações em Ferramentaria de Moldes
A ferramentaria de moldes é um setor em constante evolução, impulsionado por avanços tecnológicos, novas demandas do mercado e a busca contínua por eficiência e sustentabilidade. Neste artigo, vamos explorar as principais tendências e inovações que estão moldando o futuro da ferramentaria de moldes, destacando as mudanças que estão melhorando a qualidade, eficiência e a sustentabilidade na fabricação.
Uma das inovações mais significativas na ferramentaria de moldes é a impressão 3D, também conhecida como manufatura aditiva. Essa tecnologia tem revolucionado a forma como os moldes são projetados e fabricados. A impressão 3D permite a criação de protótipos rapidamente, possibilitando testes e ajustes no design antes da fabricação final. Essa abordagem reduz significativamente o tempo de desenvolvimento e os custos associados ao processo tradicional de usinagem. Além disso, a impressão 3D permite a fabricação de geometrias complexas que seriam difíceis ou impossíveis de criar usando métodos convencionais.
A automação e a robótica também estão desempenhando um papel crucial nas inovações em ferramentaria de moldes. A utilização de robôs em processos de montagem, inspeção e manutenção tem se tornado cada vez mais comum. A automação não apenas acelera a produção, mas também aumenta a precisão e reduz a possibilidade de erro humano. Por exemplo, robôs equipados com sensores avançados podem realizar inspeções em tempo real, garantindo que os moldes atendam às especificações de qualidade exigidas antes de serem colocados em operação.
A integração de inteligência artificial (IA) e big data está se tornando uma tendência emergente na ferramentaria de moldes. A implementação de sistemas baseados em IA pode fornecer insights valiosos sobre o desempenho dos moldes e prever falhas antes que elas ocorram. Isso permite que as empresas adotem uma abordagem de manutenção preditiva, otimizando a programação de manutenção e minimizando o tempo de inatividade. Além disso, a análise de dados coletados durante o processo de produção pode levar a melhorias contínuas nos designs de moldes e na eficiência dos processos.
A sustentabilidade é uma preocupação crescente em todas as indústrias, incluindo a ferramentaria de moldes. As empresas estão começando a adotar práticas mais sustentáveis, como o uso de materiais recicláveis e biodegradáveis na fabricação de moldes. Sua implementação não apenas reduz o impacto ambiental, mas também atende à demanda crescente dos consumidores por produtos ecologicamente corretos. Além disso, o desenvolvimento de processos de fabricação que minimizam o desperdício de material e energia está se tornando uma prioridade para os fabricantes de moldes.
Outra tendência importante é a miniaturização de moldes. Com o crescimento da demanda por produtos menores e mais complexos, o design de moldes também está mudando. Molde de injeção menores podem oferecer vantagens significativas, como redução de custos de material e maior flexibilidade na produção. Essa miniaturização exige uma nova abordagem no design e na fabricação, incentivando a inovação em técnicas de usinagem e montagem.
A utilização de simulação de moldagem é uma prática que tem se intensificado na ferramentaria. Softwares de simulação permitem que engenheiros e designers visualizem como o material se comportará uma vez que for injetado no molde. Essa tecnologia ajuda a identificar possíveis problemas antes mesmo da construção do molde, economizando tempo e recursos. A simulação torna o processo de design mais eficiente e ajuda a garantir que os moldes criados sejam otimizados para produção.
Além disso, as empresas estão investindo em treinamento e desenvolvimento de pessoal para acompanhar as mudanças tecnológicas e mantê-los atualizados sobre as melhores práticas na fabricação de moldes. O desenvolvimento de competências técnicas nas equipes é crucial para garantir que a transição para novas tecnologias seja bem-sucedida, mantendo a competitividade das empresas em um mercado em rápida evolução.
Por último, as parcerias e colaborações dentro da indústria estão promovendo o compartilhamento de conhecimento e a aceleração da inovação. As empresas estão se unindo com universidades, centros de pesquisa e startups para explorar novas tecnologias e desenvolver soluções inovadoras para os desafios da ferramentaria. Essa colaboração pode levar à criação de novos processos e melhorias significativas na eficiência e na qualidade.
Em resumo, a ferramentaria de moldes está passando por transformações significativas impulsionadas pela tecnologia e pela necessidade de atender a um mercado em constante mudança. A impressão 3D, automação, inteligência artificial, sustentabilidade, miniaturização, simulação de moldagem e colaborações são apenas algumas das tendências e inovações que estão moldando o futuro deste setor. À medida que essas tecnologias se tornam mais acessíveis e integradas nos processos de fabricação, podemos esperar uma evolução contínua que melhorará não apenas a eficiência, mas também a qualidade e a sustentabilidade na produção de moldes de injeção.
Ao longo deste artigo, abordamos a importância da Ferramentaria moldes de injeção e como ela é essencial para a eficiência e precisão na fabricação de peças na indústria. Desde a escolha dos materiais até os processos de produção, as inovações e as práticas de manutenção, cada aspecto contribui para a melhoria contínua da produtividade e qualidade dos produtos finais. Com o entendimento das vantagens e dos cuidados necessários, as empresas podem maximizar a vida útil de seus moldes, reduzir custos e atender à crescente demanda por produtos de alta performance. Convidamos você a refletir sobre como essas informações podem ser aplicadas em seu contexto e como a adoção de novas tecnologias pode impulsionar sua produção. Seja você um profissional da área ou apenas um entusiasta, o conhecimento sobre ferramentaria de moldes de injeção é crucial para navegar no competitivo cenário industrial atual.