Fábrica de Usinagem: Qualidade e Precisão em Cada Peça
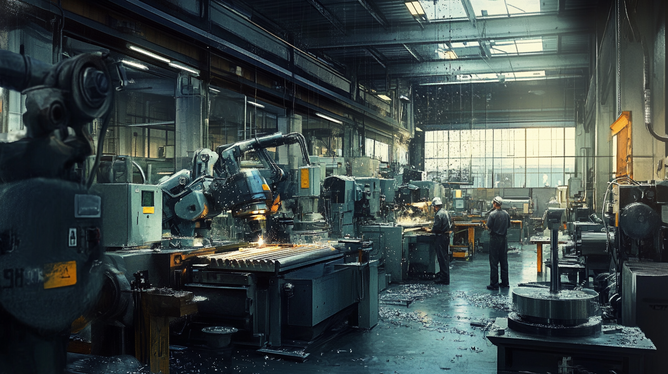
Por: Antonio - 24 de Dezembro de 2024
Fábrica de usinagem é sinônimo de precisão e qualidade na produção de peças. Neste artigo, vamos explorar como esses estabelecimentos operam, desde o processo de usinagem até as vantagens de contar com uma infraestrutura adequada. Se você deseja entender melhor a importância desse setor e como ele pode beneficiar seus projetos, continue lendo e descubra insights valiosos sobre o mundo da usinagem.
Processo de Usinagem: Passo a Passo
A usinagem é um dos processos de fabricação mais essenciais na indústria moderna, permitindo a produção de componentes e peças com alta precisão e controle de qualidade. Nesse artigo, vamos detalhar o processo de usinagem, abordando as etapas e técnicas principais envolvidas. Desde a preparação até a finalização, cada fase é crucial para garantir que as peças atendam às especificações exigidas. Vamos explorar esse processo em detalhes.
1. Planejamento do Projeto
O primeiro passo em qualquer processo de usinagem é o planejamento. Neste estágio, os engenheiros e designers colaboram para criar um modelo CAD (Desenho Assistido por Computador) da peça que será usinada. Esse modelo deve incluir todas as dimensões, tolerâncias e características especiais que precisam ser atendidas.
Além disso, o planejamento envolve a seleção dos materiais adequados. Os materiais comuns utilizados na usinagem incluem metais como alumínio, aço e latão, mas também podem incluir plásticos e compósitos. A escolha do material impacta diretamente na usabilidade da peça e em seu custo de produção.
2. Preparação da Máquina
Após o planejamento, o próximo passo é a preparação da máquina de usinagem. Existem diferentes tipos de máquinas usadas no processo, incluindo tornos, fresadoras e retiradores. Cada uma delas tem suas funcionalidades específicas e é escolhida de acordo com o tipo de peça que está sendo produzida.
Os operadores da máquina carregam as ferramentas de corte necessárias conforme o modelo e o tipo de material. As ferramentas precisam ser afiadas e calibradas corretamente para garantir um corte preciso. Essa preparação é vital, pois ferramentas inadequadas podem resultar em acabamentos ruins ou até mesmo danos à peça usinada.
3. Configuração da Máquina
Com a máquina e as ferramentas preparadas, o operador configura a máquina de acordo com as especificações do projeto. Isso inclui a definição das velocidades de corte, avanço e profundidade de corte. Configurações inadequadas podem resultar em falhas no processo, desgaste excessivo da ferramenta ou danos à peça.
Durante essa fase, são feitas medições precisas para garantir que a peça esteja alinhada corretamente. O uso de equipamentos de medição de alta precisão é fundamental para garantir que tudo esteja ajustado conforme as especificações do CAD.
4. Processo de Usinagem
Com a máquina configurada, inicia-se o processo de usinagem propriamente dito. Dependendo do tipo de usinagem, existem diferentes técnicas que podem ser aplicadas, como fresagem, torneamento, furação e retificação.
- Fresagem: Nessa técnica, uma ferramenta de corte rotativa remove material da superfície do componente, formando um perfil ou contorno desejado.
- Torneamento: Usado principalmente para peças cilíndricas, o torneamento envolve a rotação da peça enquanto uma ferramenta de corte é aplicada, removendo material em uma direção radial.
- Furação: Consiste em criar furos em uma peça, podendo utilizar diferentes tamanhos e profundidades conforme a necessidade do projeto.
- Retificação: Uma técnica de acabamento que utiliza uma roda abrasiva para melhorar a precisão dimensional e a qualidade da superfície da peça.
Durante essa fase, é importante monitorar constantemente o desempenho da máquina e a qualidade da peça. Isso pode envolver a medição do componente em várias etapas do processo, garantindo que ele permaneça dentro das tolerâncias especificadas.
5. Acabamento da Peça
Após a usinagem, o próximo passo é o acabamento da peça. O acabamento pode incluir técnicas como polimento, anodização, pintura ou revestimentos especiais, dependendo da aplicação e do ambiente em que a peça será utilizada.
Este estágio é vital, pois um bom acabamento pode melhorar não só a estética, mas também a durabilidade e resistência da peça. Por exemplo, peças que estarão expostas a um ambiente corrosivo podem precisar de um revestimento adicional para proteção.
6. Controle de Qualidade
Com a peça finalizada, entra em cena o controle de qualidade. Esse processo garante que a peça atende a todas as especificações de projeto e tolerâncias estabelecidas inicialmente. Os inspetores usam ferramentas de medição precisas, como paquímetros e micrômetros, para verificar as dimensões e a qualidade da superfície.
Caso sejam identificadas não conformidades, a peça pode ser reenviada para ajustes ou um novo processo de usinagem, dependendo da natureza do problema. Esse rigor no controle de qualidade assegura que apenas peças que atendem aos padrões exigidos cheguem ao cliente final.
7. Embalagem e Envio
Depois de passar pelo controle de qualidade, a peça é embalada para transporte. A embalagem deve ser feita de forma a proteger a peça durante o transporte, evitando danos durante o deslocamento. Embalagens adequadas também incluem informações sobre a peça e instruções especiais de manuseio, se necessário.
Uma vez embalada, a peça está pronta para envio ao cliente ou para ser integrada a um produto maior, dependendo das necessidades da fabricação. Esse passo final é crucial, pois assegura que os itens cheguem ao seu destino em perfeitas condições.
Conclusão
O processo de usinagem é complexo e requer precisão em cada etapa. Desde o planejamento do projeto até a entrega final, todas as fases têm um impacto significativo na qualidade do produto final. Entender essa sequência de operações ajuda na identificação de potenciais melhorias e inovações no processo, contribuindo para uma produção mais eficiente e eficaz.
A usinagem é, de fato, uma arte e uma ciência que continua a evoluir, incorporando novas tecnologias e técnicas para atender às crescentes demandas da indústria.
Vantagens de Ter uma Fábrica de Usinagem
Ter uma fábrica de usinagem pode trazer inúmeras vantagens para empresas que atuam em diferentes setores. À medida que a demanda por peças precisas e de alta qualidade aumenta, estabelecer uma usina de usinagem torna-se uma estratégia viável e lucrativa. Neste artigo, vamos explorar as principais vantagens de possuir uma fábrica de usinagem, abordando desde a eficiência operacional até a possibilidade de atender às necessidades específicas dos clientes.
1. Precisão e Qualidade
A principal vantagem de ter uma fábrica de usinagem é a capacidade de produzir peças com alta precisão e qualidade. A usinagem é um processo que permite tolerâncias mínimas e acabamentos superficiais impecáveis.
Com tecnologia avançada, as máquinas utilizadas nas fábricas de usinagem conseguem realizar cortes extremamente precisos, o que é essencial em indústrias que exigem componentes que se encaixem perfeitamente, como as automobilística e aeroespacial.
A capacidade de garantir que cada peça atenda a padrões rigorosos de qualidade minimiza as chances de falhas em produtos finais, aumentando a confiança do cliente na marca e reduzindo custos associados a retrabalhos.
2. Flexibilidade na Produção
Outra grande vantagem é a flexibilidade que uma fábrica de usinagem oferece na produção. As máquinas podem ser ajustadas e configuradas para produzir uma variedade de peças, desde protótipos únicos até grandes lotes de produção.
Esse nível de flexibilidade permite que as empresas atendam rapidamente a demandas variáveis do mercado. Por exemplo, numa situação onde um cliente solicita uma alteração em um projeto, uma fábrica de usinagem pode atender a esse pedido rapidamente, criando um novo protótipo ou ajustando o processo produtivo conforme necessário.
3. Redução de Custos a Longo Prazo
Embora o investimento inicial em uma fábrica de usinagem possa ser alto, a longo prazo, os custos de produção podem ser reduzidos significativamente. Com a produção interna, as empresas podem evitar gastos com fornecedores externos, além de reduzir prazos de entrega.
A eliminação da dependência de terceiros para a fabricação de componentes também diminui riscos associados a interrupções na cadeia de suprimentos, como atrasos e flutuações de preços. Isso se traduz em um melhor controle financeiro e em uma capacidade de planejamento mais eficiente.
4. Maior Controle sobre o Processo de Produção
Uma das vantagens mais significativas de ter uma fábrica de usinagem é o maior controle sobre todo o processo de produção. Isso inclui o controle dos insumos, maquinário, qualidade e prazos de entrega.
Quando as empresas produzem suas próprias peças, elas conseguem monitorar cada aspecto do processo, garantindo que todas as normas e padrões sejam seguidos. Esse controle adicional também possibilita a implementação de melhorias contínuas nos processos, resultando em produtos melhores e mais eficientes.
5. Personalização de Produtos
A capacidade de personalizar produtos é um dos atrativos mais importantes de uma fábrica de usinagem. Em vez de depender de produtos padronizados, as empresas podem criar peças sob medida que atendem exatamente às necessidades e especificações de seus clientes.
A personalização não se limita apenas às dimensões, mas também pode incluir acabamentos, tratamentos de superfície e materiais específicos. Isso torna a fábrica de usinagem um aliado estratégico na diferenciação de produtos, permitindo que as empresas se destaquem em um mercado competitivo.
6. Inovação e Desenvolvimento de Novos Produtos
Ter uma fábrica de usinagem também abre portas para inovação e desenvolvimento de novos produtos. Com acesso direto ao processo de produção, as empresas podem testar rapidamente ideias e conceitos, reduzindo o tempo entre planejamento e execução.
A possibilidade de realizar protótipos em um ambiente controlado permite que as equipes de engenharia e design experimentem diferentes abordagens e tecnologias, resultando em inovações que podem transformar o mercado. Essa agilidade é essencial para se manter competitivo em um mundo empresarial em constante evolução.
7. Melhoria da Comunicação e Relação com Clientes
Quando uma empresa tem sua própria fábrica de usinagem, a comunicação com os clientes melhora consideravelmente. Os feedbacks sobre produtos podem ser incorporados rapidamente no processo de produção, permitindo ajustes e melhorias de acordo com as necessidades do cliente.
Além disso, a capacidade de desenvolver soluções customizadas em resposta a solicitações específicas fortalece o relacionamento entre a empresa e seus clientes, aumentando a lealdade e a satisfação.
8. Acesso a Tecnologias Avançadas
Fábricas de usinagem frequentemente investem em tecnologias de ponta, como máquinas CNC (Controle Numérico Computadorizado) e software avançado de design. Essas tecnologias permitem automatizar e otimizar processos, resultando em uma produção mais eficiente e precisa.
Além disso, o investimento em tecnologia não só melhora a qualidade do produto final, mas também facilita a capacitação da equipe e a adoção de práticas mais sustentáveis e eficientes. À medida que a indústria avança para a Indústria 4.0, a integração de tecnologias digitais na usinagem é fundamental para se manter competitivo.
9. Redução de Tempo de Entrega
Com uma fábrica de usinagem, as empresas conseguem reduzir consideravelmente o tempo necessário para entregar produtos aos clientes. Ao evitar a dependência de fornecedores externos e controlar todo o processo de produção internamente, os prazos de fabricação se tornam mais previsíveis e confiáveis.
A melhoria nos tempos de entrega resulta em maior satisfação do cliente e também pode aumentar as oportunidades de negócios, pois as empresas são vistas como mais confiáveis e responsivas às necessidades do mercado.
10. Sustentabilidade e Responsabilidade Social
Investir em uma fábrica de usinagem também pode oferecer vantagens relacionadas à sustentabilidade. Com um controle maior sobre os processos, as empresas podem implementar práticas mais sustentáveis, como a redução de desperdícios, a reciclagem de materiais e a adoção de tecnologias menos poluentes.
Além disso, a responsabilidade social corporativa pode ser aperfeiçoada por meio do controle da cadeia de suprimentos e da certificação dos fornecedores, promovendo práticas éticas e sustentáveis ao longo de toda a operação.
Conclusão
Em resumo, ter uma fábrica de usinagem traz inúmeras vantagens que vão desde a precisão e qualidade até a flexibilidade e personalização. Essas características não só aumentam a competitividade das empresas, mas também contribuem para um ambiente de negócios sustentável e inovador.
A implementação de uma fábrica de usinagem é, portanto, uma estratégia inteligente para qualquer organização que busque crescer na indústria moderna, adaptando-se às necessidades do mercado e se diferenciando de seus concorrentes.
Tipos de Máquinas Utilizadas em Usinagem
O processo de usinagem é fundamental na fabricação de componentes de precisão, e para isso são utilizadas diversas máquinas especializadas, cada uma com suas características e aplicações. Neste artigo, vamos explorar os principais tipos de máquinas utilizadas em usinagem, detalhando suas funcionalidades, vantagens e as aplicações mais comuns. Entender as diferentes máquinas é essencial para escolher a melhor tecnologia para atender às necessidades específicas de cada projeto.
1. Torno Mecânico
O torno mecânico é uma das máquinas mais tradicionais e amplamente utilizadas na usinagem. Ideal para peças cilíndricas, o torno usa uma ferramenta de corte que remove material da peça giratória, permitindo criar diâmetros e formas específicas.
Os tornos mecânicos podem ser manuais ou automáticos, sendo os automáticos mais eficientes para produções em larga escala. Eles são utilizados em diversas indústrias, incluindo automotiva, aeronáutica e de ferramentas. Alguns dos tipos de tornos incluem:
- Torno convencional: Utilizado principalmente para pequenas produções e peças únicas.
- Torno CNC: Controlado por computador, capaz de realizar cortes complexos com alta precisão.
A versatilidade do torno o torna uma ferramenta indispensável em uma fábrica de usinagem, permitindo a criação de uma ampla gama de peças, desde eixos até suportes e componentes rotativos.
2. Fresadora
A fresadora é outra máquina essencial no processo de usinagem. Utiliza uma ferramenta de corte rotativa que remove material da peça, permitindo a criação de superfícies planas, contornos e furos. Existem diferentes tipos de fresadoras, incluindo:
- Fresadora vertical: Com a mesa de trabalho posicionada verticalmente, é ideal para operações que exigem cortes profundos e de precisão.
- Fresadora horizontal: Possui a ferramenta de corte posicionada horizontalmente, adequado para cortes em formas específicas e em grandes blocos de material.
- Fresadora CNC: Controlada por computador, oferece alta precisão e a capacidade de realizar cortes complexos em um único ciclo de produção.
As fresadoras são amplamente utilizadas em indústrias de fabricação de ferramentas, moldes, e na produção de componentes eletrônicos. A versatilidade e a precisão das fresadoras as tornam um ativo valioso em qualquer fábrica de usinagem.
3. Máquinas de Perfuração
As máquinas de perfuração são projetadas especificamente para criar furos de diversos tamanhos em uma variedade de materiais. Elas são amplamente utilizadas em situações onde a precisão em furos é essencial, como na fabricação de componentes mecânicos e estruturas.
Existem diferentes tipos de máquinas de perfuração, entre elas:
- Máquina de furar convencional: Comumente utilizada para furos simples, onde a precisão não é crítica.
- Furadora de coluna: Oferece maior estabilidade e força, ideal para peças maiores e mais resistentes.
- Máquina de perfuração CNC: Proporciona alta precisão e é adequada para furos complexos, controlados por computador.
A escolha da máquina de perfuração depende das especificações do projeto e do tamanho da peça a ser trabalhada.
4. Retificadora
A retificadora é uma máquina utilizada para obter acabamentos superficiais de alta qualidade e precisão em peças usinadas. Ela utiliza uma roda abrasiva para remover material, permitindo alcançar tolerâncias muito apertadas. As retificadoras são frequentemente utilizadas em indústrias que exigem acabamentos de alta qualidade, como a automotiva e relógios.
Os tipos de retificadoras incluem:
- Retificadora plana: Utilizada para criar superfícies planas e uniformes.
- Retificadora cilíndrica: Usada para dar forma e acabamento a peças cilíndricas.
- Retificadora de interior: Projetada para retificar superfícies internas, como furos em tubos e eixos.
O uso da retificadora é essencial para garantir que as peças usinadas tenham um acabamento adequado, aumentando a durabilidade e a funcionalidade dos componentes.
5. Máquinas de Corte a Laser
As máquinas de corte a laser são uma tecnologia moderna que tem se mostrado muito eficaz na usinagem. Elas utilizam um feixe de laser altamente concentrado para cortar materiais com precisão milimétrica. Este método é ideal para uma variedade de materiais, incluindo metais, plásticos e até madeira.
Entre os benefícios das máquinas de corte a laser estão:
- Precisão: Cortes muito finos e detalhados são possíveis com mínima margem de erro.
- Versatilidade: Capazes de trabalhar com diferentes tipos de materiais e espessuras variadas.
- Menor necessidade de acabamento: O corte a laser proporciona acabamentos quase prontos, reduzindo o tempo necessário para o pós-processamento.
Devido à sua eficiência e precisão, as máquinas de corte a laser são amplamente utilizadas na indústria de fabricação de placas, serralheria e produção de componentes eletrônicos.
6. Máquina de Eletroerosão (EDM)
A eletroerosão, ou EDM (Electrical Discharge Machining), é um processo que utiliza descargas elétricas para remover material de uma peça. É uma técnica que permite a usinagem de formas complexas e intrincadas que seriam difíceis ou impossíveis de alcançar com ferramentas de corte convencionais.
As máquinas de eletroerosão são especialmente úteis na produção de moldes e matrizes de alta precisão. Existem dois principais tipos de máquinas EDM:
- EDM por fio: Utiliza um fio condutor para realizar cortes em formas complexas, ideal para peças delicadas e moldes.
- EDM por penetração: Utiliza uma ferramenta que molda a peça por meio de descargas elétricas, sendo adequada para trabalhos que exigem um alto nível de facão.
A eletroerosão é altamente valorizada em indústrias como a automobilística e a de eletrônicos, onde a complexidade das peças requer processos de usinagem avançados.
7. Máquinas de Usinagem por Ultrassom
A usinagem por ultrassom é uma técnica inovadora que combina a usinagem tradicional com ondas ultrassônicas para aumentar a eficiência do corte. Essa tecnologia é particularmente útil para materiais duros ou quebradiços, como cerâmicas e compósitos.
Algumas das vantagens da usinagem por ultrassom incluem:
- Aumento da vida útil da ferramenta: As vibrações ultrassônicas reduzem o atrito, prolongando a vida útil das ferramentas.
- Acabamentos superiores: Permite acabamentos de alta qualidade em materiais difíceis de usinar.
- Menor força de corte: Reduz a força necessária para o corte, minimizando o desgaste da peça.
Essa tecnologia é especialmente interessante em setores como a medicina, onde componentes sofisticados são necessários, e em eletrônicos, onde a precisão é imperativa.
8. Equipamentos de Montagem e Manipulação
Além das máquinas de usinagem em si, uma fábrica não estaria completa sem equipamentos de montagem e manipulação. Esses equipamentos auxiliam no transporte e na fixação de peças durante o processo de usinagem.
Alguns exemplos incluem:
- Gabaritos e fixadores: Projetados para garantir que a peça fique corretamente posicionada durante a usinagem.
- Conveyors: Utilizados para mover peças de uma estação de trabalho para outra.
- Robôs industriais: Podem ser integrados ao processo para automatizar a manipulação e o transporte de peças, aumentando a eficiência.
9. Máquinas de Corte de Plasma
As máquinas de corte de plasma são uma alternativa eficaz ao corte a laser e são usadas principalmente em metais. Esses equipamentos utilizam um arco elétrico para ionizar o gás, criando um jato de plasma que pode cortar materiais com espessura variada.
A tecnologia de corte a plasma é valorizada por:
- Suporte a materiais mais espessos: Ideal para cortar materiais até 50 mm de espessura.
- Velocidade de corte: O processo é rápido, aumentando a produtividade.
- Custo-benefício: Menor custo em comparação ao corte a laser para grandes espessuras.
As máquinas de corte de plasma são amplamente utilizadas em setores como construção, metalurgia e fabricação de estruturas metálicas.
10. Conclusão
Em resumo, o conhecimento sobre os diferentes tipos de máquinas utilizadas na usinagem é crucial para qualquer fábrica de usinagem. Cada máquina tem suas características únicas e é projetada para atender a necessidades específicas de produção. Desde tornos e fresadoras até tecnologias inovadoras como o corte a laser, a escolha correta da máquina pode impactar diretamente a eficiência, qualidade e custo da produção.
Empresas que conhecem as opções disponíveis e selecionam as máquinas que melhor se adequam a seus processos e produtos podem não só melhorar seus resultados, mas também garantir a satisfação dos clientes e a competividade no mercado.
garantir consistentemente a qualidade de produtos e serviços.Além da ISO 9001, outras certificações específicas para setores, como a AS9100 para a indústria aeroespacial ou a IATF 16949 para a indústria automotiva, podem ser exigidas. A adesão a essas normas implica em processos sistemáticos e auditáveis, que ajudam a identificar e resolver problemas antes que eles afetem a produção.
3. Metodologias de Controle de Qualidade
Uma abordagem eficaz para garantir a qualidade na usinagem é a implementação de metodologias de controle de qualidade que monitorem e avaliem continuamente o processo de fabricação. Algumas das metodologias mais comuns incluem:
- Inspeção Dimensional: A medição das dimensões das peças usinadas em várias etapas do processo ajuda a identificar desvios e garantir que cada peça esteja dentro das especificações exigidas.
- Controle Estatístico de Processos (CEP): Utiliza ferramentas estatísticas para monitorar e controlar o processo de usinagem, permitindo a detecção precoce de variações e melhorando a estabilidade do processo.
- Auditorias Internas: Realizar auditorias periódicas nos processos de usinagem assegura que o sistema de gestão da qualidade esteja funcionando de acordo com os padrões estabelecidos.
- Técnicas de Melhoria Contínua: Metodologias como Six Sigma, Lean Manufacturing e Kaizen são frequentemente utilizadas para identificar ineficiências e reduzir desperdícios, melhorando assim a qualidade do produto final.
4. Inspeção de Materiais e Equipamentos
Antes de iniciar o processo de usinagem, a qualidade dos materiais utilizados é essencial para garantir que as peças finalizadas atendam aos padrões exigidos. É importante realizar inspeções nos materiais recebidos para verificar se cumprem as especificações e se estão livres de defeitos que possam comprometer a integridade do produto.
Além disso, o estado das máquinas e ferramentas utilizadas no processo de usinagem deve ser constantemente monitorado. Ferramentas desgastadas ou danificadas podem impactar negativamente a qualidade das peças usinadas. Manutenção preventiva regular e calibração de equipamentos são práticas essenciais para garantir que as máquinas operem nas condições ideais.
5. Mapeamento do Processo de Usinagem
Outra prática eficaz para garantir a qualidade é o mapeamento do processo de usinagem. Envolve a definição clara de cada etapa do processo, permitindo identificar todos os pontos críticos e as interações entre eles. Este mapeamento pode incluir:
- Fluxograma do Processo: Um diagrama que ilustra cada etapa do processo de usinagem, facilitando a visualização e identificação de possíveis gargalos.
- Identificação de Pontos de Controle: Estabelecer pontos de verificação ao longo do processo onde a qualidade pode ser inspecionada e as ações corretivas podem ser tomadas rapidamente.
- Análise de Causa Raiz: Em caso de falhas, investigar a causa raiz permite implementar ações corretivas efetivas e evitar que o problema ocorra novamente.
6. Treinamento e Capacitação da Equipe
Os colaboradores desempenham um papel crucial na manutenção da qualidade na usinagem de peças. Treinamentos regulares e programas de capacitação são indispensáveis para garantir que todos compreendam a importância da qualidade e saibam operar as máquinas corretamente.
Um bom programa de treinamento deve incluir:
- Conhecimento técnico: Formação sobre os processos de usinagem, os tipos de máquinas e ferramentas e as normas de qualidade.
- Práticas de segurança: A segurança deve ser um foco primordial em todas as operações para proteger os colaboradores e minimizar interrupções no processo de usinagem.
- Estímulo à melhoria contínua: Incentivar os colaboradores a propor melhorias nos processos pode resultar em inovações que aumentem a eficiência e a qualidade.
7. Controle de Processos e Registro de Dados
O controle de processos envolve o monitoramento contínuo das condições durante a usinagem, incluindo variáveis como temperatura, pressão e velocidade de corte. Esses dados podem ser coletados e analisados para identificar tendências que impactam a qualidade.
O uso de sistemas de gestão de qualidade que permitam a coleta e análise de dados em tempo real é cada vez mais comum. Registros detalhados permitem o rastreamento da produção, facilitando a identificação de problemas e garantindo a conformidade com os padrões de qualidade.
8. Testes e Validação das Peças Usinadas
Após a usinagem, as peças devem passar por testes e validações para assegurar que atendem às especificações e funcionalidade esperadas. Isso pode incluir:
- Testes de Dimensões: Usar instrumentos de medição para validar que as dimensões da peça estão dentro das tolerâncias especificadas.
- Testes Funcionais: Realizar ensaios para verificar se a peça funciona corretamente em sua aplicação real, especialmente em setores críticos.
- Testes de Durabilidade: Colocar as peças sob condições de uso para avaliar seu desempenho a longo prazo e a resistência a falhas.
9. Feedback do Cliente e Melhoria Contínua
O feedback dos clientes é um recurso valioso para melhorar a qualidade das peças usinadas. As empresas devem estar sempre abertas a ouvir as opiniões e sugestões de seus clientes, utilizando essas informações para identificar áreas de melhoria.
Implementar processos de feedback sistemáticos, como pesquisas de satisfação ou reuniões periódicas com clientes, contribui para manter um diálogo aberto e uma relação de confiança. Quando o feedback é analisado e incorporado nos processos, torna-se um poderoso motor de melhoria contínua.
10. Futuro da Qualidade na Usinagem
À medida que a indústria avança para a Indústria 4.0, a qualidade na usinagem continuará a evoluir com a integração de tecnologias digitais, como IoT (Internet das Coisas) e inteligência artificial. Essas tecnologias permitirão monitoramento e controle em tempo real, aumentando a precisão e a eficiência dos processos de usinagem.
A digitalização dos processos também proporcionará uma análise de dados mais robusta, permitindo uma abordagem proativa para identificar problemas potenciais antes que afetem a produção.
Conclusão
A qualidade e o controle na usinagem de peças são fatores críticos que impactam diretamente a satisfação do cliente e a competitividade da empresa. A implementação de práticas eficazes de controle de qualidade, juntamente com investimento em tecnologia e capacitação da equipe, pode levar a um aumento significativo na eficiência operacional e na qualidade do produto final.
Empresas que priorizam a qualidade na usinagem estarão melhor posicionadas para atender às crescentes demandas do mercado, garantindo sucesso contínuo em um ambiente empresarial cada vez mais desafiador.
A usinagem é um componente fundamental na indústria moderna, garantindo a produção de peças com alta precisão e qualidade. Ao longo deste artigo, exploramos as diversas operações dentro de uma fábrica de usinagem, desde os processos envolvidos até as vantagens que uma infraestrutura bem estabelecida pode oferecer. Compreender esses aspectos é vital para qualquer profissional ou empresa que busca otimizar sua produção e atender às crescentes demandas do mercado. A usinagem não apenas contribui para resultados impressionantes, mas também representa uma oportunidade de inovação e personalização em projetos. Ao considerar a implementação ou melhoria de uma fábrica de usinagem, é crucial reconhecer a importância de práticas de qualidade e controle, que garantem não apenas a satisfação do cliente, mas também o sucesso a longo prazo em um ambiente competitivo.